What are the Compressor Wheel Variations?
As turbochargers develop, operating conditions have altered significantly. Turbochargers are spinning faster than ever before and subjected to higher temperatures.
As a result, this has led to significant development in compressor wheel design to cope with ever changing conditions.
Flatback: Earliest compressor wheel design and still used by some manufacturers.
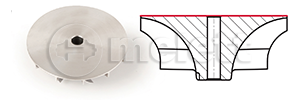
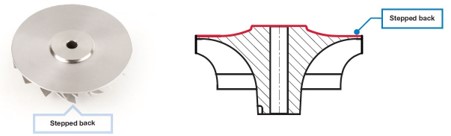
Superback: This design was introduced due to the increased speeds which turbochargers rotate, because of the speed increase the force on the compressor wheel increases significantly, in particular the exducer diameter of the compressor wheel suffered the most. This is the point which rotates the fastest and is therefore under the most stress. The Superback reinforces the back face of the compressor wheel preventing the compressor wheel tearing from the bottom up.
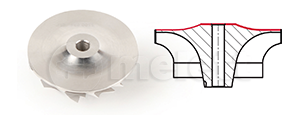
Deep Superback: An exaggerated design of the Superback, generally used on more recent applications. The theory is, this is due to the increasing rotational speeds of the turbo.
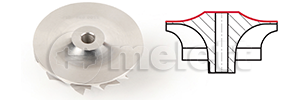
Deep Superback – Extended tip: This design promotes greater airflow providing a faster boost response at lower engine speeds. The extended tip design increases the efficiency of the Superback compressor wheel at higher boost pressures.
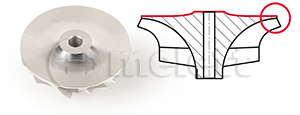
Extended Tip - Compressor Wheel
- This design promotes greater airflow providing a faster boost response at lower engine speeds
- The extended tip design increases the efficiency of the compressor wheel at higher boost pressures
- Extended Tip Technology (shown in red) to get a smaller wheel to perform like a larger wheel
- This feature amplifies the boost pressure and flow capabilities for a given wheel size
Other Types of Compressor Wheels
Boreless
- Small amount of thread which goes about half way up
- These are used on applications that have increased load
- Stronger design
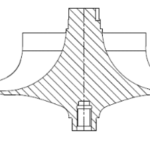
Threaded
- Thread which goes all the way up
- These are used on applications that have increased load
- Don’t have to source shaft nut
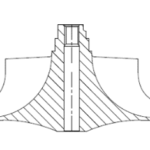